A pdf is available for download here.
Table of Contents
Akua Pin Press

Akua pin press
High cost option, around $250 new. This press is essentially a small diameter etching press printing drum, with pressure applied manually, by hand, rather than mechanically, by press. The commercially produced pin press is a 20 inch wide, flat surfaced roller used to apply high pressure across a broad, flat area. The crescent-shaped handles allow for comfortable, ergonomic printing and act as a stand when the press is not in use.
Media: Best for drypoint intaglio, collagraph, monotype and monoprint
Works well for light pressure, planographic (flat) or low relief printing processes, such as monotype or monoprint, drypoint intaglio, collagraph, kitchen or polyester plate lithography.
Links:
Baren or Spoon
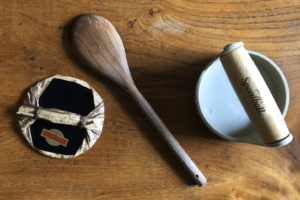
A selection of barens, from drawcutinkpress.com
Low cost option. Time intensive for each print (up to 45 minutes per small intaglio print). Requires high craft skills for relief, and very high craft skills for monotype, kitchen lithography and intaglio, along with an abundance of patience. No size limitations.
A range of spoons and barens are needed to apply pressure, depending on needs of media. For relief, where the surface ink is transferred from the matrix to the substrate, wooden spoons, rice paddles and wooden drawer pulls work well. For intaglio, where below the surface ink is transferred, metal spoons and bone folders work well to apply the concentrated, high pressure needed to create a full, clean transfer. Note that any equipment used for art making should no longer be used for food preparation as contamination can occur from the pigments and solvents that may be hazardous to health if ingested.
Media: Best for relief
Baren or spoon printing is a traditional method to print relief prints, and works well for relief printing, traditionally using thin eastern paper. Moderate success is possible with monotype and kitchen or polyester plate lithography, using thin western or eastern paper. Moderate to low success is possible with small intaglio plates, using thin western or eastern paper.
Links:
Belinda Del Pesco, Printing a drypoint with a spoon
Drawcutinkpress.com, Printing relief with a baren or spoon
Sarah Whorf, instructions to Make a Toothpick Baren, low cost with excellent results
Casters
Low cost option, about $5 new. Casters can be found or bought new. Many casters will require modification to work well for printing. The concept is to create as high psi, or pressure, as possible per square inch, to replicate the pressure of a printing press. Printmaker Sheila Goloborotko discovered this solution as she experimented with affordable ways for students to continue making work at home without a press during the COVID-19 pandemic.
Similar to spoon printing relief prints, manual pressure is used by hand to roll the caster firmly over the printing packet to transfer the ink from the printing matrix to the dampened substrate. Time, labor, moderate skills, a high level of craft and patience are required. Once the initial setup is created and technical trouble shooting occurs, it will be possible to print even moderate sized images, or multi-layer images, using this method.
Media: Best for intaglio and monotype
Works well for intaglio printing, and can be used for monotype and kitchen or polyester plate lithography. If used for relief printing, a stable registration jig is needed to keep the block and paper stationary.
Links:
Sheila Goloborotko’s video tutorial on printing drypoints by hand using a caster
Michelle Rozic’s video tutorial on printing drypoint by hand using a caster
Recommended Casters:
3 in. polyurethane heavy duty rigid caster, rated 275 lb. (220 grit wet/dry sandpaper will be needed to flatten the caster prior to printing)
Shepherd Hardware 9781 3-Inch Cast Iron Rigid Caster, 250-lb Load Capacity (already flat, no modification needed)
Credit Card Imprinters
Low to moderate cost option, $20-$60 new from office and bank supply retailers, or second-hand.
Modified credit card imprinters are small, portable devices that work well for relief printing. With moderate skill, basic hand tools and picture framing wire, the rollers can be adjusted and the support can be converted to a flat press bed to allow for printing small relief blocks. Once converted, the presses can easily be used for small printing. The machines are durable as they are made for commercial use. The small size will limit printing size.
Media: Best for relief
Works best for relief printing and relief printing collagraph.
Links:
Sarah Whorf’s video tutorial on printing with a credit card machine
Instructables post by Becca Rose
Dancing
A low cost option with varying results. Works well for proofs and single plate prints. All that is needed is a flat, hard surface floor, smooth socks, some good dance music and a little patience.
Media: Best for collagraph
Works well for collagraph printing and relief printing, using thin western or eastern paper. I imagine monotype, and kitchen or polyester plate lithography would also print moderately well with this method.
Links:
Camilla Taylor dance printing a collagraph
Die Cut Machine
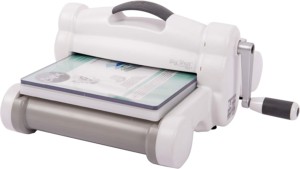
Sizzix Big Shot
High cost option, about $75+ new. Die cut machines can be purchased second hand. Coupons are also available for many craft stores. Lowest initial time investment needed for setup as the press is already created for horizontal motion through the rollers, so no conversion is needed. Die cut machines are easier to use than a pasta machine as the rollers are already positioned to roll a bed through horizontally. Some trial and error is required to get quality results. Some die cut machines have a fixed height roller, so it is necessary to gather boards of different thicknesses to adjust the height of the roller. On fixed height die cutters pressure must be adjusted by adding or removing material from the bed to change the distance between the roller and bed. Once initial testing is complete, it is easy to reproduce consistent printing results. Size limitation based on width of die cut machine.
Media: Best for relief, monotype, kitchen lithography and drypoint intaglio
Works well for relief printing, monotype, kitchen or polyester plate lithography, and intaglio, using thin western or eastern paper. Can be used for letterpress printing with solar plates and a bed support.
Links:
L.S. King’s overview of the Big Shot Sizzix as a printing press
Rebecca Ravenhill’s overview of the Big Shot Sizzix as a printing press
Recommended Die Cut Machines:
Big Shot Sizzix: The brand most recommended by printmakers using die cutters as presses. The Big Shot comes in two sizes. The width of the die cutter will determine the widest material you are able to print.
Xcut Xpress: Similar to the Big Shot but has a dial to adjust the roller height. Difficult to find in the U.S. Available for purchase from Handprinted UK along with additional long bed, though currently not shipping to US. May be able to find on second hand sites.
Gelatin Monoprinting Plates
Low to moderate cost option. These plates are a great introduction to monotype printing. The flat gelatin surface easily releases pigment to the printing paper. The plates are great for achieving textural prints and for using stencils. Advanced and professional printmakers may find the plates limiting. Precise detail is difficult to achieve due to the soft nature of the plate.
Plates can be purchased commercially or made at home using gelatin and glycerin.
Media: Only for monotype
Suitable only for monotype printing, due to the nature of the plate.
Links:
Gelli Arts Gel Printing Plates
Kim Herringe: Gelatin Plate Printmaking Recipe
Hand Presses
Moderate cost option. Similar to the caster, this hand press works using a flat surfaced roller to apply high pressure in a concentrated area. These presses are more ergonomic in that they are created for hand printing. The rollers are wider and flatter and so the transfer will be more even and take less time than with caster printing.
Media: Best for intaglio and monotype
Works well for intaglio printing, monotype and kitchen or polyester plate lithography. If used for relief printing, a stable registration jig is needed to keep the block and paper stationary.
Links:
Sashas’ Palm Press: More rollers, made for lithography and works well for intaglio and monotype (note, no longer available for purchase, can modify the design to DIY)
Pocket press DIY instructions pdf download
Pasta Makers/Polymer Clay Rollers
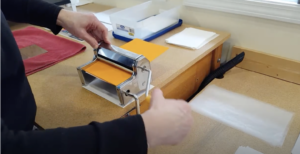
From Janet Ballweg’s video on converting pasta makers for printmaking
Moderate cost option, about $25-$50 new. Pasta makers can be purchased second hand from thrift stores or online second-hand marketplaces. Many people have pasta makers sitting unused in their kitchen cupboards, asking around for a donation of an unused pasta maker, before purchasing new, may save you some money and free up a friend or family member’s cabinet space. Any pasta maker will work as a press. The cheaper options are typically poorer quality construction, while the more expensive options are higher quality construction.
Pasta makers feed material through vertically. To use vertically, flexible matrices must be used to allow the sandwich of matrix, printing paper, and packing to curve through and out from beneath the rollers.
For printmaking use, it works best to turn pasta makers sideways, allowing for flat, or horizontal feed, of the material through the rollers, and clamping the press down to keep it from moving while rolling the material through. Time, labor, tools, and moderate skills required to convert pasta maker for use as a horizontal printing device. Pressure is adjusted by changing the dial. Pasta makers typically have 9 thickness settings. Those with carpentry skills are encouraged to build a frame around the pasta machine to give full support as the bed rolls through the rollers. Some trial and error is required to get quality results. Once initial testing is complete, they are able to reproduce consistent printing results. Size limitation based on the width of pasta maker.
Note that any equipment used for art making should no longer be used for food preparation as contamination can occur from the pigments and solvents that may be hazardous to health if ingested.
Media: Best for monotype, kitchen lithography and drypoint intaglio
Works well for monotype, kitchen or polyester plate lithography, and intaglio, using thin western or eastern paper.
Links:
A great round up of pasta makers/polymer clay rollers. The review is written for polymer clay artists but I imagine the press attributes reviewed translate well for printmaking needs.
Janet Ballweg’s series of videos, including modifying an Amaco craft press to print horizontally.
Annie Day’s inking and printing a waterless litho plate with a pasta press.
Michelle Rozic’s converting an Atlas 150 to horizontal printing.
Recommended Pasta Makers:
Amaco craft clay machine $25-30
Cheapest option, poor quality construction. This is a good option if you would like a press rather than printing by hand with a spoon, are patient with minor frustrations while working, and think you may not use this frequently. Available for purchase from many craft and art supply retailers.
Higher quality construction. From my online research, this is the best of both worlds when it comes to balancing cost with durability. The cutter slides off and the bottom plate easily comes off with a screw driver and matching bit for printing horizontally.
3D Printed Presses
Low to high cost option, $10-$100, depending on if resources are available to 3D print a press and purchase the additional parts, or if a preprinted press is bought.
Open Press Project
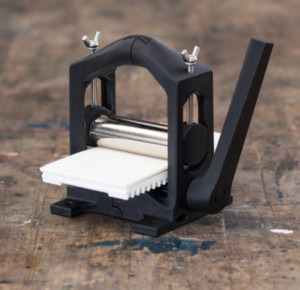
From Open Press Project
In 2018, Martin Schneider and Dominik Schmitz created an open source 3D printed etching press. They first beta tested with ten prototype iterations before releasing the final plans. Their goal was to make printing accessible to the masses by removing the prohibitive costs of traditional printing presses. Lightweight, portable, inexpensive and durable, these presses can print paper up to 3 x 5 ¾ inches. Since its debut, thousands of artists across the globe have printed their own presses with high quality final print results.
Media: Best for relief, intaglio, monotype, monoprint, kitchen and pronto plate lithography
Anything that can be scaled down and printed on a traditional etching press can be printed on this open source printing press.
Links:
Zine Machine Hi-Bred
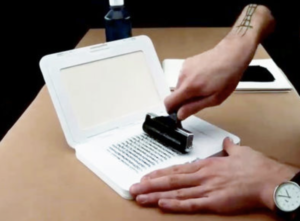
From Gigazine
Released in 2021, the Zine Machine is a 3D printed tiny version of a block printing press. 3D printed or hand carved blocks fit inside the chase. The block is inked, printing paper loaded, and the Zine Machine is closed with firm pressure applied to the outside to transfer the ink to paper. The print examples shown online have mixed results with irregular ink transfer, which may be solved with the addition of packing.
Media: Only for relief
Works well for 3D printed or hand carved relief blocks. May work with solar plates.
Links:
Zine Machine Plans and Instructions
Zine Machine Printing Tutorial
Tortilla Press
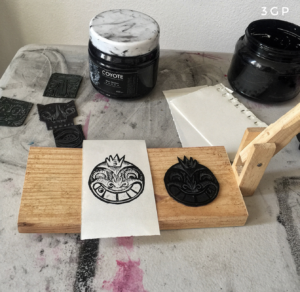
From 3 Gatos Press
Low to moderate cost option, about $5-$50 depending on size of tortilla press. Lining the top with compressed felt will help to achieve more even transfer of ink to paper. The print size is limited to the diameter of the tortilla press. Note that any equipment used for art making should no longer be used for food preparation as contamination can occur from the pigments and solvents that may be hazardous to health if ingested.
Media: Best for relief
Works well for unmounted linoleum relief printing, using thin western or eastern paper. Low success possible with monotype, kitchen or polyester plate lithography, or intaglio, using thin western or eastern paper.
Links:
3 Gatos Press, tortilla press relief prints